Home : CNC :
[ comment | link | top ]
...I believe the specifics have changed, the following may or may not help. If you get prompted to setup the X-Carve; use the pictured settings (click to enlarge) and choose no homing, manual spindle control and no z-probe.
If the X-Carve is cutting too deep, the lead screw setting is wrong and needs to be set to Acme (coarser thread/less revolutions than M8). I'm not sure what is causing it, someone using the default/wrong settings or the X-Carve loosing its settings and falling back to the default settings.
[ comment | link | top ]
The dust collector shoe swings out of the way for easy bit changes and provides good cut visibility.
[ comment | link | top ]
The fixture is a combination square and wasteboard that allows routing multiple pieces using the same home position. While the square is not particularly square, it does allow for reasonably accurate repetitive (re)positioning. The example is one of three marble mazes that were routed with a bullnose bit and then repositioned and through cut with a straight bit.
The fixture has 5mm holes on 75mm centers (same as the X-Carve) that allow positioning and clamping anywhere on the table. There are also some special 2 hole clamps for clamping 1/4 and 1/2" stock to the fixture (example stock is 3/4)... The smaller square/wasteboard has two possible positions to allow more flexible clamp placement. The fixtures are stored in the lower right hand cabinet.
[ comment | link | top ]
Generally, cutting wood works best with straight two flute bits and plastic with single flute up-cut spiral bits. Down cut spiral bits can provide cleaner cuts in wood and may be worth the extra cost in some applications. Compression (up/down spirals) are only beneficial when the first pass is deep enough to get past the up spiral portion - not possible w/ the X-Carve.
Inventables bit articles:
Carving Bits 101 - Bit Basics
Carving Bits 201 - Feeds, Speeds, and V-Bits
[ comment | link | top ]
X-Carve
X-Carve and Easel howto topics.
Usage Basics
- Mount you material to the wasteboard
- Manually move the router to the left front corner of the workpiece
- Check/adjust the X axis so that it is parallel to the front of the machine
- Use the Z knob and a piece of paper to adjust the Z axis
- Turn on the X-Carve "CNC" switch to set the project origin (X,Y,Z 0)
- Position the dust shoe and tighten the top knob
- Click the Carve button
- Turn on the "Spindle" switch when asked if the router is on
- Turn off the "Spindle" switch for tool changes (NOT the CNC switch)
- Select the appropriate Easel Workpiece
- Only move the X and Y axes in custom increments, e.g. 100mm/4.0"
- Raise Z as needed and change the tool
- Use the same custom increments to return X and Y to the corner of the material
- Use increasingly smaller Z increments to get the new tool down to the material
- Click the Carve button and, when asked, select use New position (NOT Last position)
- Turn on the "Spindle" switch when asked if the router is on
[ comment | link | top ]

Machine Setup
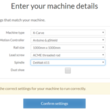
If the X-Carve is cutting too deep, the lead screw setting is wrong and needs to be set to Acme (coarser thread/less revolutions than M8). I'm not sure what is causing it, someone using the default/wrong settings or the X-Carve loosing its settings and falling back to the default settings.
[ comment | link | top ]

Dust Collector
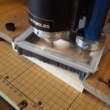
- Loosen the ...top (3/22) knob and swing the shoe out of the way
- Insert/tighten the bit and set its start location/height
- Turn on the CNC controller to lock the stepper motors
- Swing the shoe over the bit until the bit is centered in the hole/shoe
- Set the shoe plate just high enough to clear all clamps/screw heads.
- Insure that the space between the router body and shoe is >= depth of cut.
- Tighten the top knob.
[ comment | link | top ]

Repetitive Cut Fixture
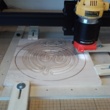
The fixture has 5mm holes on 75mm centers (same as the X-Carve) that allow positioning and clamping anywhere on the table. There are also some special 2 hole clamps for clamping 1/4 and 1/2" stock to the fixture (example stock is 3/4)... The smaller square/wasteboard has two possible positions to allow more flexible clamp placement. The fixtures are stored in the lower right hand cabinet.
[ comment | link | top ]

Router Bits
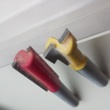
Inventables bit articles:
Carving Bits 101 - Bit Basics
Carving Bits 201 - Feeds, Speeds, and V-Bits
[ comment | link | top ]
